熱壓罐設(shè)備與傳統(tǒng)成型工藝在多個方面存在顯著的差異。以下是對這兩種成型工藝的對比分析:
一、設(shè)備結(jié)構(gòu)與原理
熱壓罐設(shè)備
結(jié)構(gòu):熱壓罐是一個具有整體加熱系統(tǒng)的大型壓力容器,一端封閉,另一端開口,內(nèi)部配有循環(huán)風(fēng)扇以實現(xiàn)熱量的均勻分布。
原理:將復(fù)合材料毛坯或預(yù)浸料用真空袋密封在模具上,然后放入熱壓罐中。通過加熱和加壓系統(tǒng),對制品進行升溫、加壓、保溫(中溫或高溫)、降溫和泄壓等處理,使其成為所需形狀和質(zhì)量的構(gòu)件。
傳統(tǒng)成型工藝
設(shè)備:傳統(tǒng)成型工藝通常使用烤箱等設(shè)備來提供固化過程中所需的高溫。
原理:將材料放入烤箱中,通過加熱使其固化成型。但烤箱通常不能提供固化過程中所需的壓力,因此可能需要配套多臺設(shè)備才能完成整個固化過程。
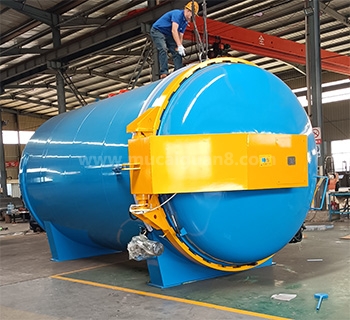
二、成型效果與適用范圍
熱壓罐設(shè)備
成型效果:
制件尺寸穩(wěn)定,重復(fù)性好。通過精確控制溫度、壓力和時間等參數(shù),可以確保制品的尺寸精度和形狀穩(wěn)定性。
力學(xué)性能可靠??芍圃炖w維體積含量高(60%~65%)的復(fù)合材料制品,這些制品具有較高的強度和剛度。
孔隙率低,樹脂含量可控。通過均勻的壓力和溫度分布,可以實現(xiàn)制品內(nèi)部的高質(zhì)量固化。
適用范圍:適用于各種工裝和形狀復(fù)雜的復(fù)合材料制品,特別是對于大型制品和復(fù)雜曲面的加工具有獨特優(yōu)勢。廣泛應(yīng)用于航空航天、汽車制造、船艇工業(yè)以及高端消費品等領(lǐng)域。
傳統(tǒng)成型工藝
成型效果:受限于烤箱的加熱方式和溫度控制精度,傳統(tǒng)成型工藝可能無法實現(xiàn)均勻的溫度分布和壓力控制,從而影響制品的成型質(zhì)量和力學(xué)性能。
適用范圍:通常適用于形狀簡單、尺寸較小的復(fù)合材料制品的固化成型。在某些特定領(lǐng)域,如汽車配件改裝等,傳統(tǒng)成型工藝仍有一定的應(yīng)用空間。
三、生產(chǎn)效率與成本
熱壓罐設(shè)備
生產(chǎn)效率:單次可以生產(chǎn)多個制品,且固化周期相對較短(盡管對于某些高溫高壓材料可能較長),因此具有較高的生產(chǎn)效率。
成本:熱壓罐設(shè)備體積大、結(jié)構(gòu)復(fù)雜,且是壓力容器,因此建設(shè)投資費用較高。同時,每次固化時都需要制備真空密封系統(tǒng),這將耗費大量價格昂貴的輔助材料(如真空袋、密封膠條等),提高了制造成本。
傳統(tǒng)成型工藝
生產(chǎn)效率:單次只能生產(chǎn)一個制品,且固化周期可能較長(因為需要等待烤箱升溫至所需溫度并保持一段時間),因此生產(chǎn)效率相對較低。
成本:雖然傳統(tǒng)成型工藝的設(shè)備成本相對較低,但由于生產(chǎn)效率低且需要配套多臺設(shè)備才能完成整個固化過程,因此整體成本可能并不低。
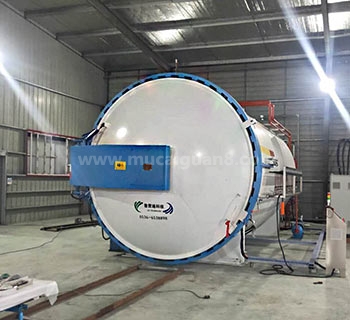
四、環(huán)保與能耗
熱壓罐設(shè)備
環(huán)保:熱壓罐成型工藝通常使用惰性氣體(如氮氣)作為加壓介質(zhì),避免了空氣自燃的危險。同時,通過精確控制溫度和壓力等參數(shù),可以減少能源消耗和廢棄物排放。
能耗:雖然熱壓罐設(shè)備在運行時需要消耗大量的電能和熱能,但由于其高效的加熱和加壓系統(tǒng)以及保溫系統(tǒng),可以降低能源浪費并提高能源使用效率。
傳統(tǒng)成型工藝
環(huán)保:傳統(tǒng)成型工藝在固化過程中可能產(chǎn)生有害物質(zhì)排放(如揮發(fā)性有機化合物等),對環(huán)境造成一定影響。同時,由于烤箱的加熱方式不夠均勻且可能產(chǎn)生熱損失,因此其環(huán)保性能相對較差。
能耗:傳統(tǒng)成型工藝在固化過程中需要消耗大量的電能和熱能,且由于加熱方式不夠高效和均勻,因此能源浪費現(xiàn)象較為嚴重。